2.4. MAKRO ve MİKRO TEST
Testler içindeki en temel basamak, malzemenin genel yapısı, kaynak dikişleri, yüzey durumları veya şekilsel etkiler gibi yüzey karakteristikleri için görsel muayene işlemidir. Kaynak birleştirme işlemleri başta olmak üzere çok yaygın bir biçimde, hemen hemen her üretimde kendisine yer bulmaktadır. Malzemelerin ve kaynakların incelenmesinde en yaygın prosesler, makro ve mikro incelemelerdir.
Kaynak kalite kontrolünde ve malzeme teknolojilerinde metalografinin önemli bir yeri vardır. Özellikle kaynak yapısını tanımlarken kaynak metali, ısıdan etkilenmiş bölge ve orijinal metal gibi üç farklı yapı ön plana çıkar. Kaynak metali ve ısıdan etkilenmiş bölge incelendiğinde, bileşim, tane boyutu ve yönlenmesi, mikro yapı ve sertlikte değişmeler görülebilir. Bu sebeple kaynaklı bölgenin mikro yapısında da önemli değişmeler gözlemlenebilir. Bununla birlikte malzemelerin mikroyapı incelemesi ise, üretim aşamasından görmüş olduğu ısıl işleme ve işletme aşamasındaki durumuna kadar bizlere bilgi veren bir testtir.
Makro ve Mikro Test, kaynaklı bir birleştirmede kaynak bölgesinden, malzemelerde ise incelenecek bölgeden alınan bir numunenin yüzeyinin kimyasallar yardımıyla dağlandıktan sonra büyütülerek mikroskop altında incelenmesiyle yapılan testtir. Yapılan işlem sonrasında makro yapıda ana metal, ısıdan etkilenen bölge ve kaynak bölgesi, mikro incelemede ise malzemelerin mikroyapıları incelenir.
Makro Test yöntemi yardımıyla, köşe kaynaklarında boğaz yüksekliği, efektif boğaz yüksekliği, alın ve köşe kaynaklarında kaynak nüfuziyeti, çatlak, gözenek vb. süreksizlikler belirlenebilir. Kullanılan programlar yardımıyla belirtilerin boyutları ve penetrasyon miktarları da incelenebilir. Mikro Test yardımıyla, malzemelerin iç yapıları, tane boyutları, taneler arası kusurlar, ısıl işlemleri, faz durumları gibi konularda bilgi edinilebilir.
Kaynak Eğitim ve Muayene Merkezimiz, Makro ve Mikro Testleriniz için tahribatlı muayene laboratuvarımızda bulunan Numune Hazırlama Cihazları, Dağlama Cihazı ve Metalografi Mikroskopları ile hizmet vermektedir.
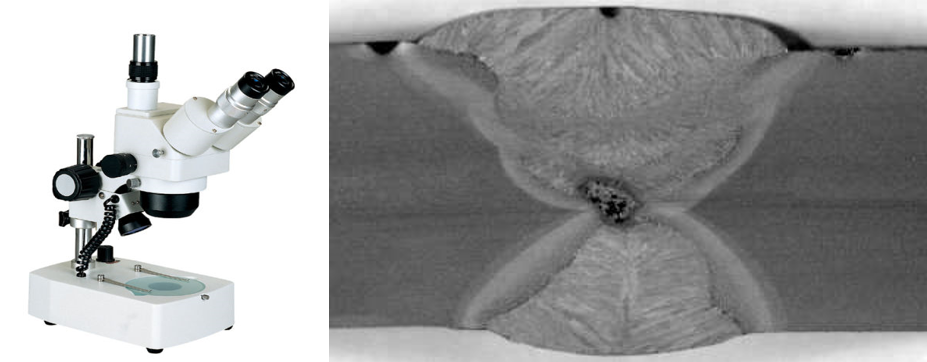
(1).jpg)
2.5. SERTLİK TESTİ
Ürün numunelerinin üzerinde yapılan en yaygın deneylerden biri, malzemenin sertliğinin ölçülmesidir. Deneyin basit oluşu ve diğer mekanik deneylere nazaran numunenin daha az tahrip edilmesini, bu deneyin yaygın olarak kullanılmasının başlıca sebeplerindendir. Diğer önemli avantajı ise, bir malzemenin sertliği ile diğer mekanik özelliklerin arasında ilişkilendirme yapılabilmesidir. Örneğin çeliklerde, çekme mukavemeti sertlik ilişkilendirilebilir; dolayısıyla numune üzerinde gerçekleştirilen sertlik deneyleri sonucunda malzemenin mukavemeti hakkında fikir edinilebilir.
Genel olarak bakıldığında sertlik izafi bir ölçü olarak karşımıza çıkmaktadır. Dolayısı ile sertlik sonuçları, malzemenin çizilmesine, kesmesine ve plastik deformasyona karşı direncine bağlanabilir. Laboratuvarlarda numunelere özel olarak cihazlarla yapılan sertlik testlerinde bulunan değerler, malzemenin plastik deformasyonuna karşı gösterdiği direnç olarak düşünülebilir.
Sertlik ölçümü, malzemeye bilinen miktardaki bir yük ile başka bir malzeme tarafından yük uygulanması, bastırılması ile ölçülebilir. Batıcı uç olarak elmas gibi sert malzemelerin kullanılmasıyla deformasyon sadece kuvvetin uygulandığı malzemede (test numunesi) sınırlı tutulur.
Vickers sertlik deneyi, tabanı kare ve tepe açısı 136° olan standartlaştırılmış piramit seklinde bir elmas ucun, değişken yükler altında numune yüzeyine batırılması sonucu bir iz oluşturma esasına dayanır. Vickers sertlik deneyinin kullanım alanı çok geniştir. Çok yumuşak ve çok sert malzemeler için uygundur.
Kaynak Eğitim ve Muayene Merkezimiz, Sertlik Testleriniz için tahribatlı muayene laboratuvarımızda bulunan HV10 Sertlik Test Cihazı ile 0.3, 0.5, 1.0, 3.0, 5.0, 10.0 kgf. yüklerde hizmet vermektedir.
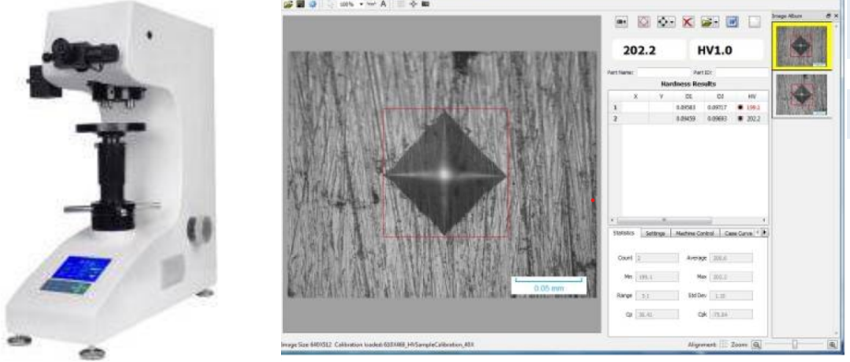
2.6. KIRMA TESTİ
Kırma testi, kaynaklı birleştirmeler üzerinden çıkartılan test numunelerinin kaynak metalinden kırılmasını sağlayıp, kırılan yüzeylerin incelenmesini sağlayan testtir. Bu testte amaç, numunenin kırılmasından sonra kırılma bölgesini incelemek ve varsa bulguları ortaya çıkarmaktır.
Genel olarak kaynak bölgesinden standartların izin verdiği ölçüde çentik açılarak gerçekleştirilir. Uygulanan kuvvet ile numunenin kaynak bölgesinden kırılması sağlanır. En temel testlerden olup özellikle iç köşe kaynaklı plakalarda hızlı bir şekilde uygulanır.
Yapılan testin ardından oluşan kırılma yüzeyleri üzerindeki iç kusurların tipleri, boyutları ve dağılımları hakkında bilgi edinmek için test gerçekleştirilir. Kırma testi ile aşağıdaki kusurlar bulunabilir;
- Gözenekler
- Çatlaklar
- Ergime noksanlıkları
- Nüfuziyet noksanlıkları
- Katı kalıntılar
Kırma testi kolay uygulanan testlerden birisidir. Kaynağın kırılma bölgesine etki edecek şekilde kuvvet uygulanması ve numunenin kaynak bölgesinden kırılması bu test için yeterlidir.
Kaynak Eğitim ve Muayene Merkezimiz, Kırma Testleriniz için tahribatlı muayene laboratuvarımızda bulunan 300 kN’luk hidrolik pres ile hizmet vermektedir.
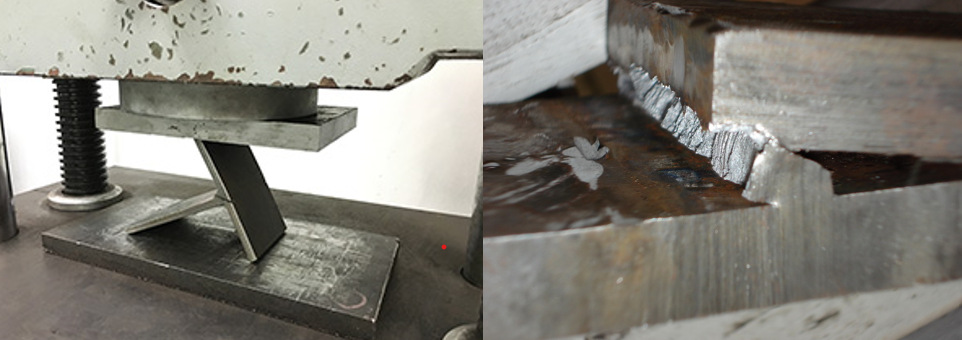
2.7. EZME TESTİ (PE)
Elektrofüzyon kaynak yönteminde kaynak, manşon veya semer mesnet içinde bulunan ısıtma rezistansları ile yapılır. Manşon veya semer mesnet içine borular yerleştirildikten sonra kaynak makinesinin uçları bağlantı elemanın delik içerisindeki rezistans uçlarına bağlanır ve rezistanslar akım ile ısıtılır. Rezistansların ısınması sonucu bağlantı elemanının et kalınlığının borunun et kalınlığından daha çok olmasından dolayı, boru cidarının ısısı, manşon cidarının ısısından daha yüksek olur. Bu ısı farkından dolayı boru içerisinde basınç oluşur. Boru üzerindeki basınç ile boru içerisinde oluşan basınç sayesinde kaynak işlemi gerçekleşir.
Ezme deneyi, PE 80 boruların, PE 100 manşon ve semer mesnet bağlantılarının ideal numune boyutlarına getirilerek bir mengene yardımı ile ezilmesi ve ardından incelenmesi prensibine dayanır. Polietilen borular için elektrofüzyon kaynağı ile üretilmiş numunelere bu test gerçekleştirilir.
Yapılan ezme işlemi sonrası kaynak bölgesinden açılmaya bakılır. Eğer kaynak bölgesinde meydana gelen açılma, standartlarda belirlenen sınırları geçiyorsa kaynaklı imalatın uygun olmadığı belirlenir.
Ezme deneyi için, kaynaktaki çatlak boyu bir elektrofüzyon birleştirmede telin ilk iki sırası arasındaki mesafeden büyük olmamalıdır. Isıtılmış eleman kaynakları için ortaya çıkan herhangi bir çatlak boru ve bağlantı elemanları arasında oluşmamalıdır.
Kaynak Eğitim ve Muayene Merkezimizde, EN 12814-4’e göre elektrofüzyon kaynağı ile birleştirilmiş manşon ve semer mesnet bağlantılarınız için ezme testi yapılmakta ve raporlanmaktadır.
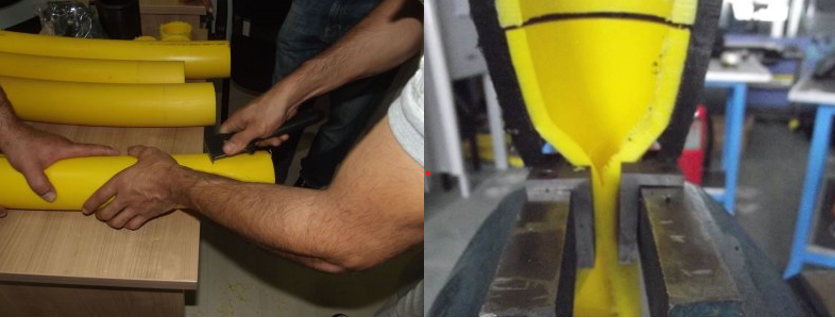
2.8. SPEKTRAL (KİMYASAL) ANALİZ
Optik Emisyon Spektrometresi veya OES, farklı türdeki alaşımlara ait metallerin elemental düzeyde bileşimini belirlemek için kullanılan, güvenilen ve yaygın olarak kullanılan bir kimyasal analiz yöntemidir.
Optik emisyon spektrometrelerle analiz edilebilecek numuneler dökümden alınan kokil numunelerle gibi külçe, kütük, cıvata, çubuk, tel ve plaka gibi ürünler de olabilmektedir.
Bu cihazla ile malzeme içerikler tam olarak ayırt edilmekte olup malzeme kalitesi belirlenebilmektedir.
Malzeme kalitesinin belirlenmesi, hem proje ve imalat aşamasında hem de işletme aşamasında değerlendirme ve analiz için çok önemli bir adımdır.
Kaynak Eğitim ve Muayene Merkezi olarak teknik hizmetlerimiz kapsamında laboratuvarımızda bulunan spektral analiz cihazı ile malzemelerin kimyasallarını tespit edebiliyor ve sonuçları yorumluyoruz.
TAHRİBATLI MUAYENE LABORATUVAR HİZMETLERİ BAŞVURULARINIZ İÇİN
kemm@mmo.org.tr
0224 443 66 11